Processes
We are expert of metal based solutions
We provide advanced solutions for automotive and industrial clients all across Europe. Our expertise spans a wide range of services, from precision engineering and manufacturing to cutting-edge technology integration.
01
Stamping
Sheet metal stamping
A wide machine park, with presses up to 800 tons.
Cutting, shaping, punching… We are experts in these processes.
Fine Blanking
20 fine blanking presses up to 600 tons.
Defta is a recognized expert of fine blanking, an advanced cutting process.
Complex tools
To adapt to its customer needs, Defta has the knowledge design, prototype, validate and maintain all sorts of tools.
Transfer tools
With always more complex parts, and with always more volumes, Defta has a lot of experience in this process from answering its automotive customer needs.
02
Assembly & Welding
As a Tier 1 automotive supplier, we are experts in design and manufacturing even the most complexes assembly processes, while striving for performance and quality.
With expertise in automated welding, including various processes like TIG, MIG, MAG, and resistance welding, as well as mechanical assembly techniques such as crimping, riveting, and clamping, we ensure precise manufacturing tailored to customer needs.
Collaborating with machine providers, we design customized machines to optimize production line efficiency based on client specifications.
03
Machining
At Defta, our proficiency lies in seamlessly integrating machining into our high-volume automated production lines.
Our machining experts provide customized solutions to meet our customers' exact requirements. Our high-speed machining centers are adapted to handle both small and large production runs.
04
Surface treatment
At Defta, we enhance the resilience and aesthetics of metal components through diverse surface treatment techniques.
Processes such as electroplating, anodizing, Epoxy paint and Zn coating are applied to increase resistance to corrosion and wear, while also adding specific finishes. Each treatment is carefully tailored to the component’s use-case, ensuring optimal performance and longevity.

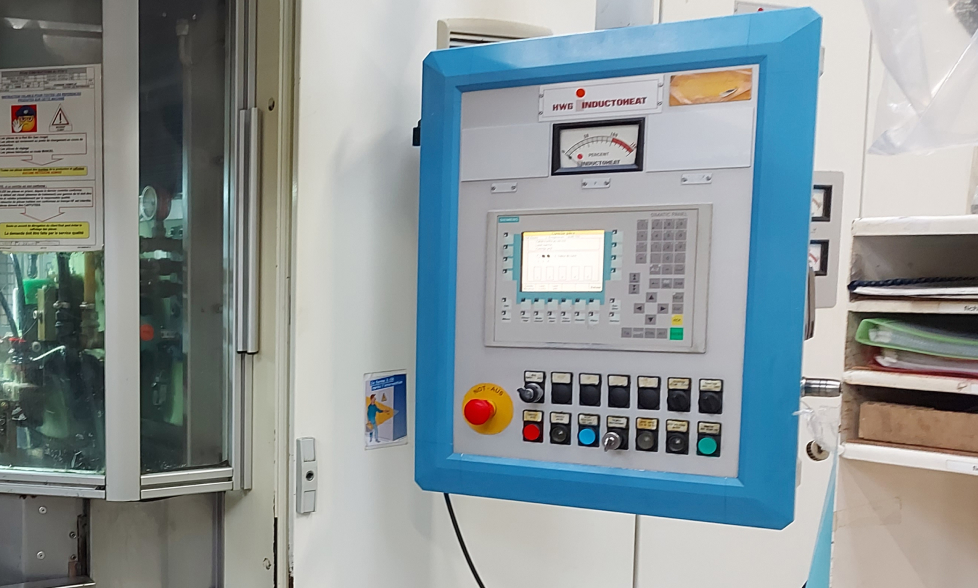
05
Heat treatment
Our heat treatment processes effectively alter the microstructure of metals, significantly enhancing their functional properties such as toughness and fatigue resistance.
Techniques including quenching and tempering are employed to achieve desired outcomes, with each procedure carefully monitored to ensure peak performance under operational stresses.
06
Overmolding
Our overmoulding services enable different materials to be fused together to create composite solutions with enhanced structural integrity and multifunctional capabilities.
This process integrates soft plastics with hard metals to produce parts that offer improved shock absorption and weather resistance, catering to industries where such traits are paramount.
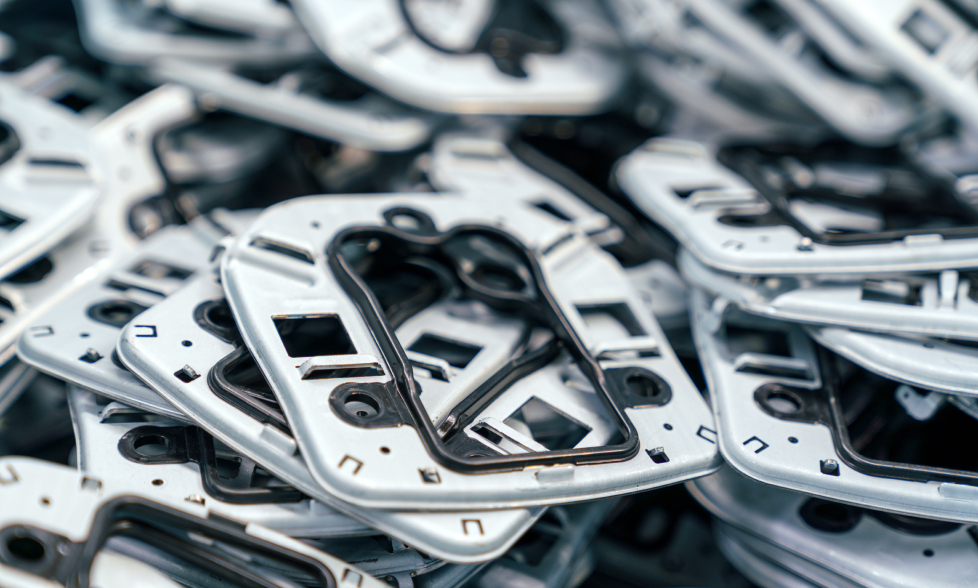
08
Aluminum die casting
Aluminum die casting is a metal-forming process that allows for the creation of complex aluminum parts. Machined aluminum parts are lightweight and capable of withstanding the highest operating temperatures. One of the most significant benefits of aluminum die casting is that it creates lighter parts with more surface finishing options than other die cast alloys. Defta has high-performance machines and masters this process.
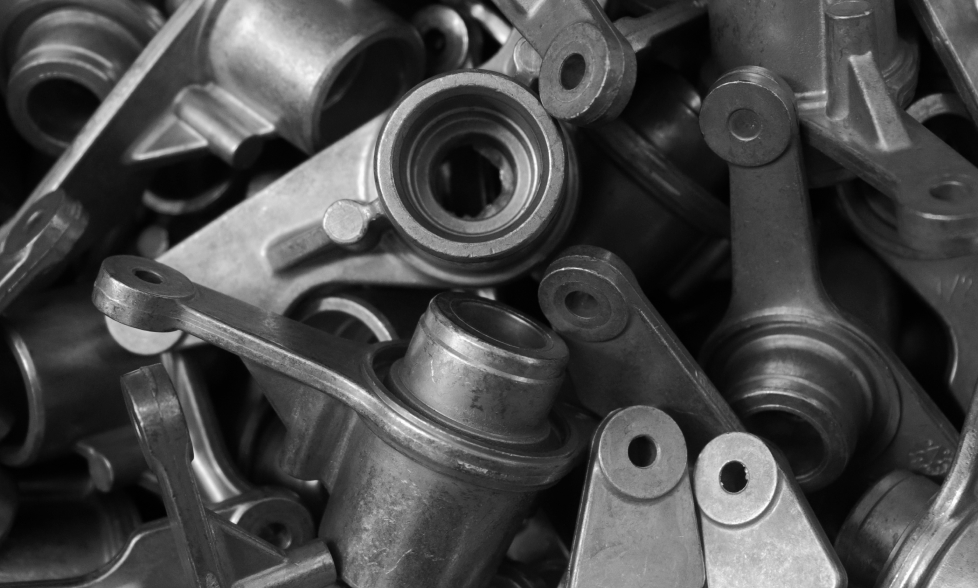
Ready to learn more?
Our team is here to assist you with any inquiries or information you may need.
Know-how
Our value-added is a determined commitment to innovation, which allows us to implement the latest market technologies in fine blanking, stamping, welding, plastic injection, heat treatments and assemblies.
Innovation
Whether it's product or manufacturing process, technical, environmental, or economic advancements, the Defta teams' appetite for innovation and continuous improvement is insatiable.